Nikola Labs Vero
Commercial / Industrial, IoT Enablement
Sensor and transponder housings for proprietary Factory 4.0 technology
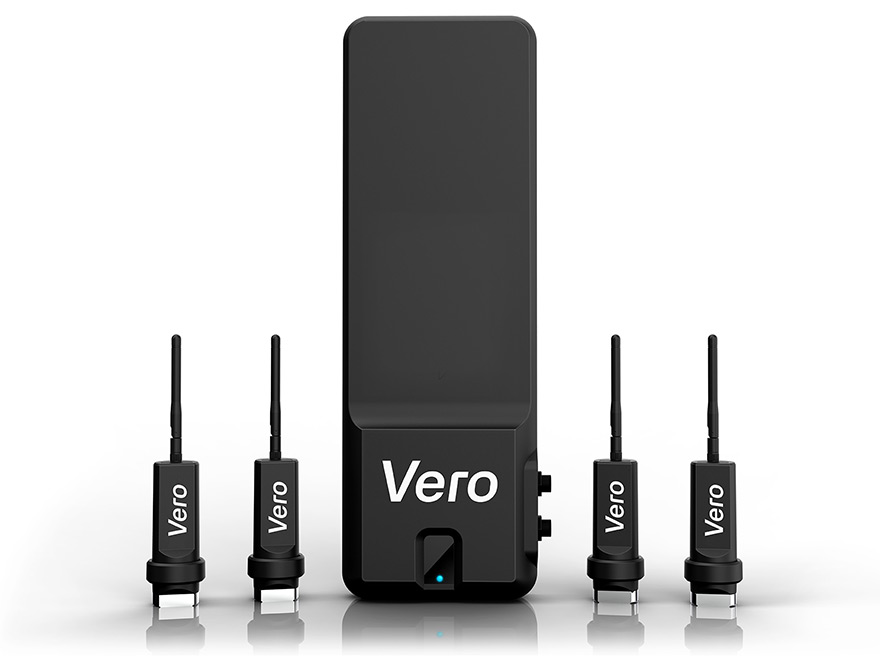
Smarter sensors, seamless maintenance
Nikola Labs (rebranded as AssetWatch®) approached Nottingham Spirk to develop the hardware needed for its PfM Sensor System.
The Vero predictive maintenance system consists of sensors and transponders and IoT cloud platform. The sensors monitor the temperature and vibrations of heavy machinery and relay data back to the transponders to help staff anticipate equipment failure.
The sensors are also equipped with tiny, proprietary INDRA chips, which convert radio frequency (RF) energy from the transponders into direct current power. This means more sensors can be used in more hard-to-reach places because there is no need to schedule downtime for battery replacement (“a maintenance program for my maintenance program,” as one factory owner put it).
The technology was developed at The Ohio State University by Dr. Chi-Chih Chen, who worked with Texas Instruments and Skyworks Solutions to reduce the chip size. Nikola Labs then turned to Nottingham Spirk for help with the product design and building critical waterproof housings and mountings.
NS worked fast and responded in time to prove value in the field. We also helped Nikola develop the proximity sensor, which shuts off the RF flow when obstructed, for instance by a person walking past it.
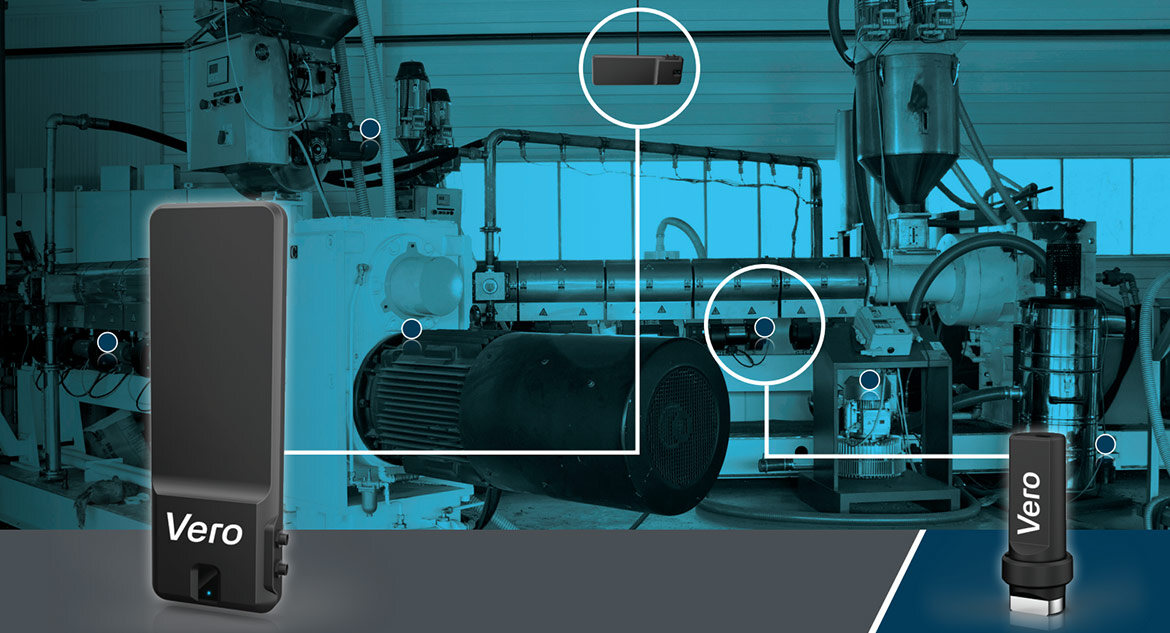
The Vero is a complete equipment health monitoring system, consisting of a transponder, sensor modules, and IoT cloud platform.
Predictive, not reactive
The PfM Sensor System is exactly what modern industry has been waiting for.
“Industry 4.0 models are based around working smarter instead of harder through networked, monitored equipment,” writes Manufacturing Focus magazine.
“Machines and facilities cannot simply be kept running until they fail and then have repairs; the upkeep on them must be constant. Twenty to thirty percent of the value of production can be lost due to downtime. To recoup these costs, industries have moved toward a model that can keep machines running and is predictive rather than reactive.”
Our Work
Medical Devices
Medtronic CardioInsight™ Vest
Developing & engineering a breakthrough medical device.